Automotive Sheet Metal
High quality sheet metal parts for automotive industry.
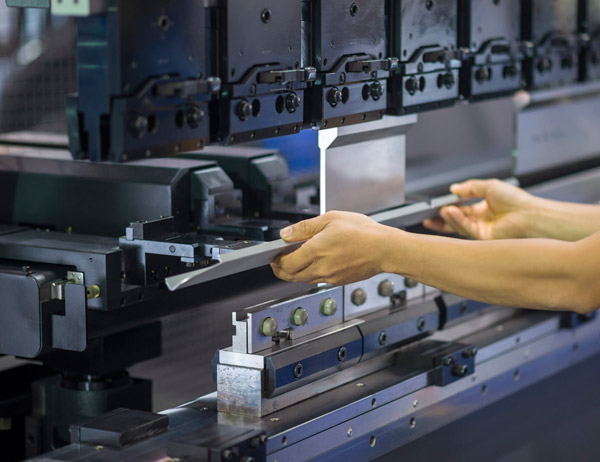
Automotive Sheet Metal
Sheet metal generally comes in three forms – aluminum, mild steel and stainless steel. Aluminum and mild steel are the most commonly used for automotive projects. The chassis, covers, engine parts, and other body parts owe their rigidity to sheet metal. We invite you to further explore our services.
Only 4 steps you can build up your business commercial sales reserve. You will receive automotive components with a classy look and no loss in strength. With immense durability and resistance, they can withstand the test of time. The corrosion resistance is also higher and thereby making them relatively maintenance-free. It helps increase the lifetime of automotive components and thereby reduces the costs incurred by servicing them.
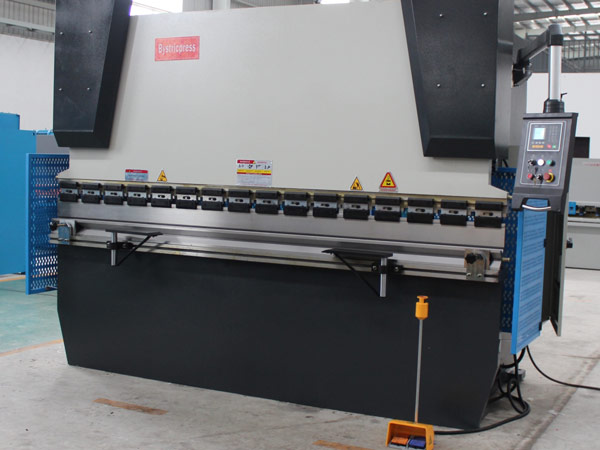
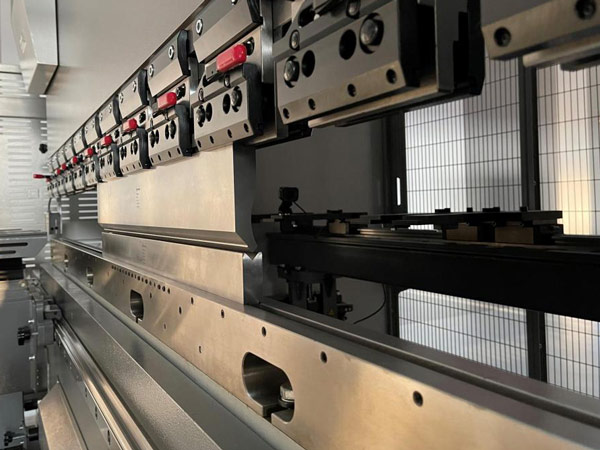
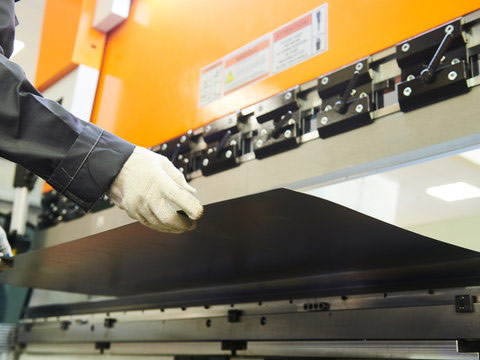
How Sheet Metal Works for Automotive Industry?
The products in the automotive and vehicle industry use a large volume of steel sheets. Those shapes are fit for the brackets, frames, chassis, plate, covers and the shields, which are covered most shapes of the car parts. It’s a perfect process for car manufacturing. The types of steel used in the automotive industry can be anywhere from stainless steel, high-strength steel, high-carbon, low-carbon, or galvanized steel for body panels.
This process provides better structural rigidity for automotive products. The grooves, ribs, or designs that are pressed into sheet metal can hold tension. Bending is another method that helps you get stronger structure. It generates more strain on the outer surface of the metal compared to the inner one. This results in the formation of cracks if you bend a piece of sheet metal past its bend radius. Sheet metal should be bent at the lowest bending radius possible.
Car Sheet Metal Parts
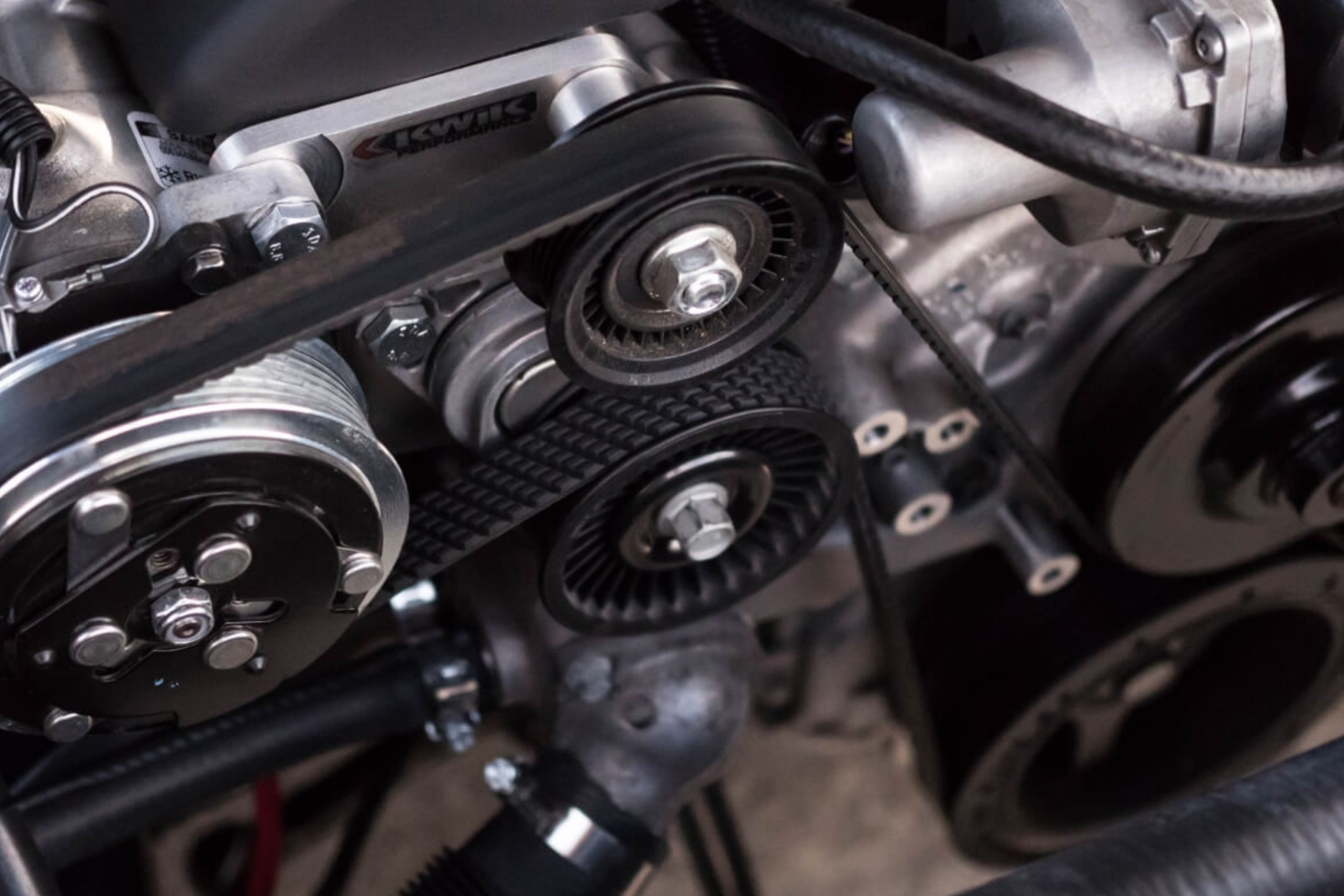
Car Body Parts
MY sheet metal provides a high-quality finish for the car body. Using our sheet metal parts can help you to achieve your design in the right way. Commonly galvanized steel is utilized in body panels.
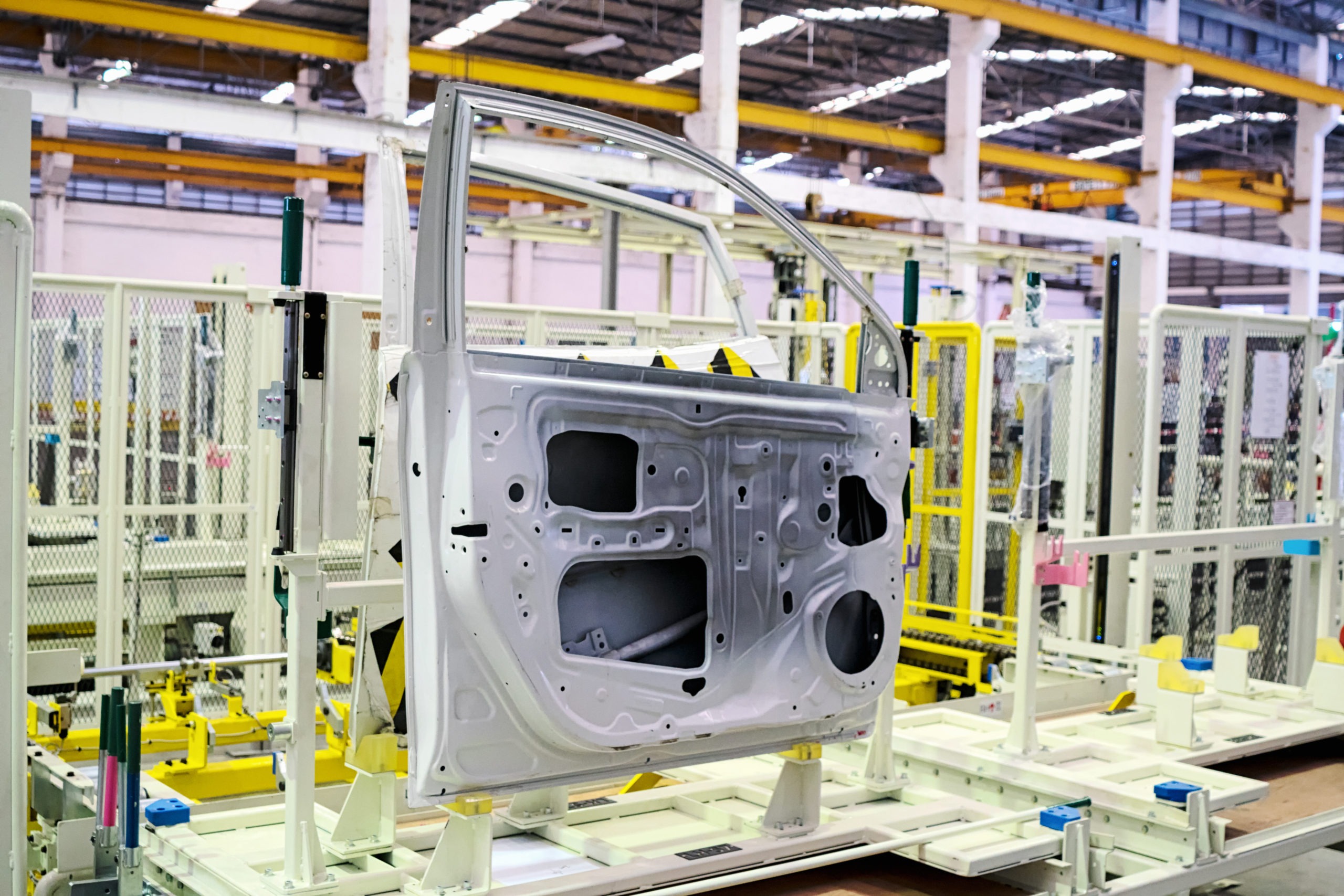
Door Parts
MY provides a series of surface finishing for your door part sheet metal. Such as a complete electrocoat primer process (ELPO).
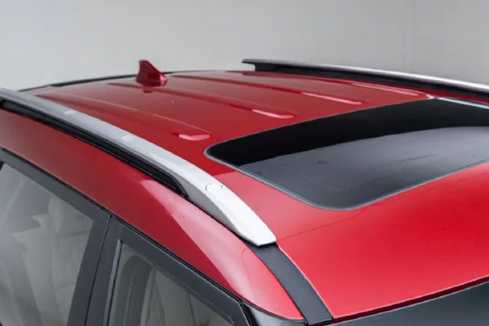
Roof Parts
It is guaranteed to feature the correct shape, size, and curvature. Fabricated using the finest grade OE gauge steel, it ensures long and seamless service.
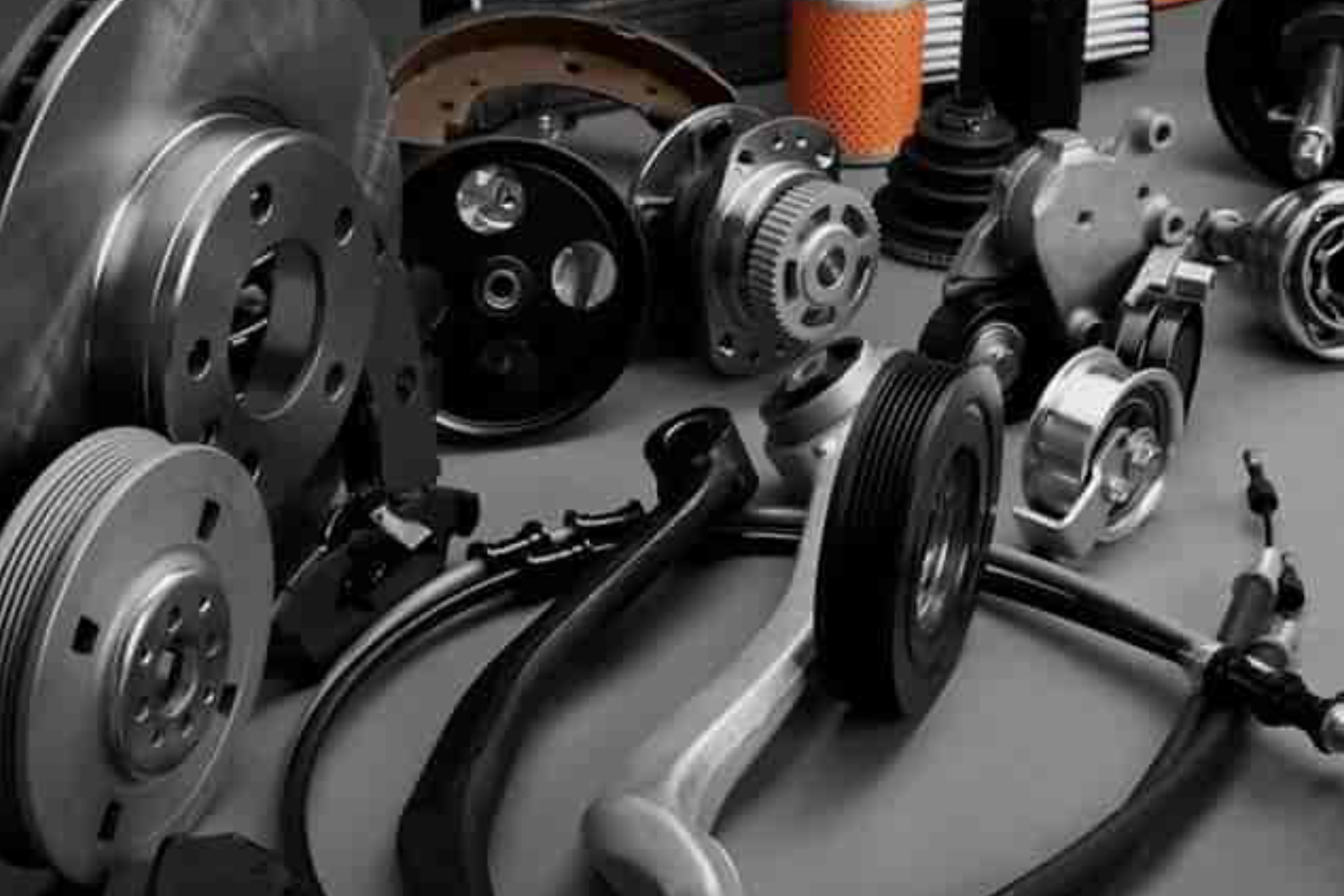
Steel Auto Parts
Floor pans, suspension control arms, leading or trailing suspension links, C-or O-section frames, catalytic converter housings, and sensor mounting brackets are numerous parts made out of sheet metal. All are in tight tolerance.
9 Main Process used in Automotive Manufacturing
- Sheet Metal Bending. Sheet metal is bent into the desired shape by applying bending stress. The sheet metal is bent so metal deformation is reached. That prevents the metal from regaining its former shape.
- Sheet Metal Curling. Curling is the process of forming a circular ring at the edge of the metal sheet to make it safer for handling. Curling can also be classified into an off-centre and an on-centre roll. Off-centre rolls have the centre above the level of the sheet, whereas on-centre rolls have the centre at the same level as that of the metal sheet.
- Deep Drawing. Deep drawing is a sheet metal forming process in which a sheet’s shape is changed to the desired shape in multiple stages using a series of dies. Punches and dies are used to create changes at every stage. Using this process, a sheet is converted into many different shapes like a fuel tank, sink, and automobile parts. Deep drawing is mostly used for large-batch
- Hydro-Forming. the metal is placed on a die, high-pressure fluid is used to shape the sheet. Since matching dies are generally not needed, hydro-forming can be used to form unconventional shapes.
- Laser Cutting. It is precise and the finish is extremely smooth. CNC machines are generally used to cut specific shapes. After feeding the program, the specific cut is carried out by laser. Laser cutting has the advantage of flexibility. When needed, changes in the required shape can be carried out easily.
- Punching. It is a very common technique for cutting holes in sheet metal. The setup consists of a punch and a punching die. There is a very small clearance between the two.
- Rolling. It is classified as hot rolling or cold rolling. In hot rolling, the temperature is around 1400 degrees Fahrenheit for steel. This can help achieve a thickness from 1/16th of an inch to 5/16th of an inch. In cold rolling, the process is carried out at room temperature. The material is washed with acid and heat treated to achieve a good finish.
- Press Brake Forming. It’s used for smaller parts making it suitable for smaller pieces along with large pieces. Thickness up to 25 mm can be easily bent and the length of the piece can go up to 6 m.
- Wheeling. Wheeling is mainly used in producing low-volume customized parts for old vehicles. It is also used for creating sheet metal parts for car prototypes and aircraft.
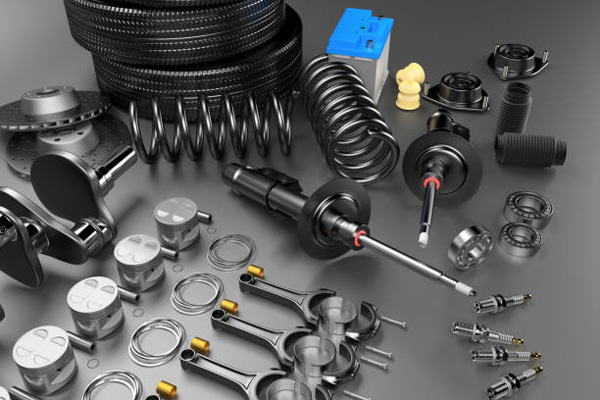
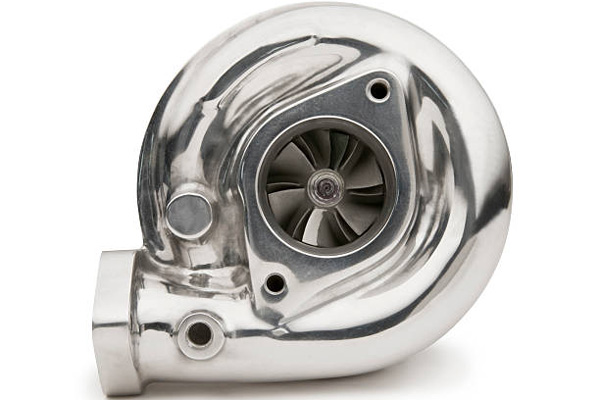
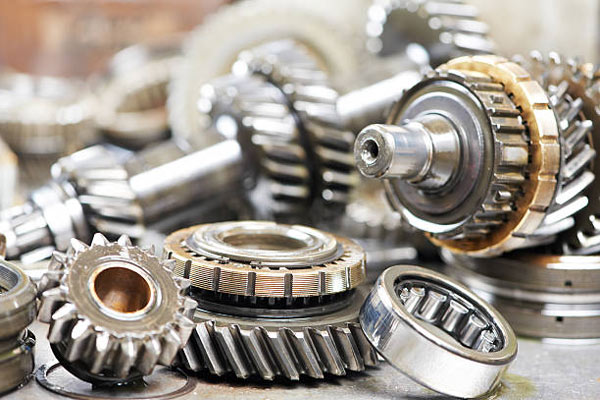
Top 3 Materials Used in Auto Manufacturing
- Mild Steel. It is an excellent material to use for parts such as car door skins. This type of sheet metal is easy to weld and unlikely to rip or tear. If you are looking for light sheet metal, mild steel is the ideal choice.
- Aluminium. Aluminium coil is widely preferred as car restoration sheet metal. Aluminum is ideal for dashboards due to the fact that it is light and relatively easy to handle. It’s fashion to use it with color anodizing.
- Stainless Steel. It is extremely resistant to oxidation and is thus very durable. Stainless steel’s high melting point makes it ideal for building and adding car parts such as brackets, panels, and tubing, as well as for interior trim pieces.